Consumers selected internationally will soon get the chance to have their shoes customized with midsoles made using data captured by wearable sensors and 3D scanners generating a full digital analysis of individual feet and motion. Shoes will be automatically engineered to a wearer's unique biomechanical and orthotic parameters representing a revolution in ultimate engineered comfort.
Within project Quant-U, the Innovation Lab ECCO collaborated with Dassault Systèmes' FashionLab, a technology incubator dedicated to the use of 3D design, simulation and collaboration applications in consumer goods and fashion, to develop a powerful self- learning system based on our own algorithms. Dassault Systèmes' cloud-based 3DEXPERIENCE platform can interpret biomechanic data into geometries for 3D printing, all without any operator intervention. Generative designs are validated through FEA simulations to ensure superior functionality. Data is captured using ECCO proprietary wearable sensors developed in collaboration with Cambridge Design Partership (Cambridge, UK) and finally combined with 3D foot scans based on the Volumental 3D scanning solution(Stockholm, SE).
3D printers
Utilising dedicated 3D printers developed by German Rep-Rap in Munich and materials from The Dow Chemical Company, medical grade silicone is 3D-printed in the form of core implants replacing the majority of the midsole polyurethane. Two years of research have been clearly proving advanced properties of this 3D printed meshes both in terms of viscoelastic performance as well as capitalizing on the unique performance of silicone in terms of durability and temperature stability. Parts created with this unique 3D printing process do not need any post production treatment or cleaning, offering a unique opportunity for their production directly in the retail setting.
Firstly, it will be a few selected customers visiting W-21 in February 2018 who can have midsoles customised. W-21 (http://W-21.nl) is an experimental ECCO Shoe Store in Amsterdam named after its location at Wolvenstraat 21. The concept is purely experimental retail and a testing environment. The moving of boundaries is a natural development for ECCO which since being established in 1963 have challenged the norms and invested in innovation across the areas of design and production.
Brain Child
The retail concept store W-21and now the Quant-U project are each a brain child of ECCO's Innovation Lab (I.LE.) situated in Amsterdam, the Netherlands. ILE is a studio, established in 2015 envisioning future concepts and designs, and where an international team of industrial designers, researchers, engineers and futurists continuously seek to disrupt and provide improvements for the footwear and leather industry.
"Throughout my experience as a designer and footwear engineer, the concept of perfect fit, perfect comfort and ultimate performance has long been an obsession", says Patrizio Carlucci, the Head of I.L.E.
The desire for perfect fit has been at the heart of footwear design for centuries and in many ways industrial solutions haven’t radically progressed since the 1920’s when the Brannock device for simultaneously measuring length and width was first introduced. To move beyond this nearly century-old 2D standard, the team at I.L.E. set themselves the challenge to expand the criteria of 'Fit', 'Comfort' and 'Performance' while remaining true to the quality and minimalism of ECCO’s Scandinavian design.
"We see a lot of activity on the subject of 3D printed footwear without a solid solution for true mass customisation from competitors. Additive manufacturing offers the chance to create bespoke parts in series but this is rarely translated in a consumer product; most likely due to the complexity of the 3D models and a lack of measuring data to begin with. To solve this, we focused heavily on the digital capture and interpretation of motion and orthotic data, then made sure this experience would be no more complicated than trying on a shoe in the store and walking for a few minutes. We truly translated more than 50 years of shoemaking experience into an algorithm" explains Patrizio Carlucci.
New approach
Besides pioneering a new approach to data capture, analysis, automated design and material development it has also been required by I.L.E. to engineer a new approach to 3D printers: adapting them to conventional retail environments. A compact (Quant – Si Quantified Silicon) printer is being already tested as a seamless element of future retail concepts and allows the custom made silicone midsoles to be printed in the store for individual consumers in near real-time.
Consumers can expect to pay in the region of 350-400 euros for a custom made, ultra-limited pair of ECCO's popular Soft 8 – Q model. The data-capture and trial period are expected to take roughly 10 minutes, with the production of the custom made Quant-U augmented midsoles taking approximately another hour.
For this experimental project, ECCO will activate in December an online enrollment process for 200 candidates in the EMEA region followed by further initiatives in Asia and in the USA towards the end of 2018.
Learn more about the project at http://quant-u.com
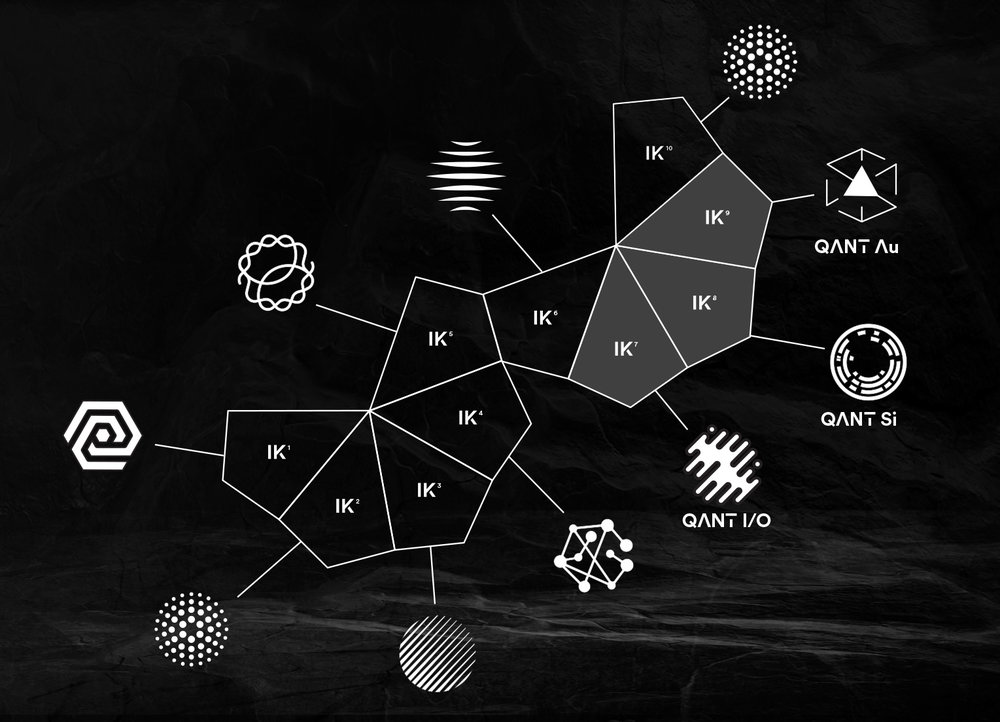